网上有很多关于智慧pos机聚合物锂电池,基于三维分层结构的锂离子电池电化学的知识,也有很多人为大家解答关于智慧pos机聚合物锂电池的问题,今天pos机之家(www.poszjia.com)为大家整理了关于这方面的知识,让我们一起来看下吧!
本文目录一览:
智慧pos机聚合物锂电池
摘 要: 本文研究采用基于三维分层结构的锂离子电池电化学-热耦合模型,分析方形电池最小单元的温度场及电流场特性,并优化极耳尺寸。恒流放电工况实验及仿真结果对比显示,模型在0.5 C、1 C及2 C倍率放电时的温度及电压曲线均与实验吻合良好,说明该模型可用于分析电池的电化学特性及热特性。研究发现随着放电倍率的增大,放电终止时刻电池最大温升以凸型曲线的趋势升高,2 C倍率放电时高达33.83 ℃;自身最大温差以凹型曲线的趋势增大,2 C倍率放电时为1.6645 ℃;垂直于隔膜方向的平均电流密度及电流密度分布的最大差值呈线性增长,2 C倍率放电终止时分别为43.62 A/m2及2 A/m2。进一步研究发现电池最大温升及最大温差与负极耳和正极耳的电阻比Sc显著相关,最优的Sc值被认为在0.875附近。当Sc<0.875时,电池最大温升及最大温差分别以1.52 ℃/Sc及5.2 ℃/Sc的速率快速下降;当Sc>0.875时,电池最大温升以0.2021 ℃/Sc的缓慢速率下降,最大温差以0.1934 ℃/Sc的速率缓慢上升。另外垂直于隔膜方向的平均离子电流密度及电流密度差值受Sc值的影响较小。
关键词: 锂离子电池;三维分层;电化学-热耦合;仿真;极耳优化
锂离子电池具备高比能量、长循环寿命等优点,被广泛用于电动汽车及储能系统领域。随着电池系统安全事故的发生,全生命周期电池安全性能研究已成为热点。电池系统温度及其均匀性是影响安全性及循环寿命的显著因素,因此电池结构优化设计及其热管理极为关键。
电池仿真是研究电池热特性的重要方法。现有电池三维结构热仿真模型包括集总参数模型及三维分层结构模型。集总参数模型认为电池为均一结构,其产热源项与空间无关。集总参数模型中产热源项获取方法包括:无电化学耦合的Bernardi模型测试,基于单粒子的电化学-热耦合模型,基于等效电路模型的电化学热-耦合模型,及基于P2D的电化学-热耦合模型。上述模型无法获得包括极耳在内的三维电势场分布,因此与之耦合的电池温度场分布及极耳结构优化等结果与真实值存在一定偏差。三维分层结构模型考虑电池铜箔、负极材料、隔膜、正极材料、铝箔等结构,并分别计算耦合的电势场和温度场。其电化学模型通常是基于P2D模型,不同的是考虑了三维空间下的活性粒子的迁移和扩散。张志超等采用分层结构模型分析了电池电势场及温度场,发现极耳连接区域的电位变化非常不均匀,靠近极耳区域的温升较大。Alipour等建立了极耳同侧分布的电池三维单层结构及分层结构模型,分析认为分层结构模型误差较单层可减少一半。另外该学者发现在大倍率放电时,正极处温升快;在1 C、3 C、5 C倍率放电时,电池表面的最大温差分别为1.1、3.5及8 ℃,说明大倍率放电时该款电池结构需改进优化。Ghalkhani等亦对同侧极耳分布电池的三维分层的电场特性及热特性进行研究,发现由于电流密度分布的不均匀,大部分的产热都集中在正极极耳附近;且极耳的位置对电场及温度场分布有显著的影响。
三维分层结构模型可获取电池三维空间内详细的电场及温度场分布,是研究电池特性、优化电池结构的较优模型。本文针对对侧极耳分布的方形铝壳电池,研究采用电化学-热耦合的三维分层结构模型,分析不同放电倍率时电池的电场及温度场特征,并优化极耳尺寸。
1 研究对象及模型1.1研究对象本文研究对象为某国产90 A·h锂离子电池,其正极材料为磷酸铁锂,负极材料为石墨,电芯采用层叠方式制造。如图1(a)所示,电池安全阀置于电池顶部;电芯负极耳由顶部引出,与外部极柱相连并与电池外壳绝缘;电芯正极耳由底部引出并与外壳焊接,正极柱设置与顶部亦与外壳焊接相连。负极耳中心位置与电池中轴线距离dneg=31.725 mm,负极耳宽度Wneg=45.5 mm,长度Hneg=15 mm;正极耳中心位置与中轴线共线,正极耳宽度Wpos=95.5 mm,长度Hpos=15 mm;正极涂布宽度Wcol=126.9 mm,高度Hcol=194.2 mm。图1(b)为电芯最小单元示意图,图示铜箔厚度LCu=3 μm及铝箔厚度LAl=7.5 μm,分别为实际厚度的一半;辊压后负极材料厚度Lneg=63 μm, 正极材料厚度Lpos=86.5 μm;隔膜厚度Lsep=16 μm。电芯总最小单元数Ncell为166。
图1 电池结构图:(a) 平行于极片方向截面图;(b) 垂直于极片方向截面图
1.2电化学-热耦合模型本文计算域为电池三维分层结构的最小电池单元,如图1(b)所示,包含带负极耳的铜箔半片,负极材料、隔膜、正极材料各一片,带正极耳的铝箔半片,忽略电池外壳及正负极柱等结构。计算域电池容量为90 A·h/Ncell,即0.5422 A·h。
1.2.1 控制方程
(1) 电极动力学方程
多孔电极界面反应产生的电流密度j可用Butler-Volmer方程[式(1)]描述,其中j0为交换电流密度,αa和αc分别为阴极和阳极的传递系数,η为电极反应产生的过电势,法拉第常数F= 96487 C/mol,理想气体常数R = 8.314 J/(mol2·K),T为温度。
(1)
交换电流密度j0计算如式(2)所示,其中k0为反应速率常数;cs,max为电极活性物质最大锂离子浓度;cs,surf为活性物质表面锂离子浓度。
(2)
反应速率常数k0与温度相关,计算如式(3)所示。其中k0,ref为参考温度下的反映速率常数;EaR为反应活化能;Tref = 298.15 K为参考温度。
(3)
公式(1)中过电势η为固相电极电势ϕs与电解液电势ϕl及电极开路电势Ueq的差值,如式(4)所示。电极开路电势Ueq由Tref温度值下参考电势Ueq,ref计算所得,如式(5)所示。
(4)
(5)
(2) 电荷守恒方程
对于固相电极,电流is计算遵从欧姆定律,如式(6)所示。其中σseff为固相电极等效电导率,与电极材料固有电导率σs、电极材料体积分数εs相关,可根据如式(7)[9]所示的Bruggeman关系计算;Sa为活性颗粒比表面积,当其为球形颗粒时,可由式(8)[9]计算,式中Rs为活性材料颗粒半径。
(6)
(7)
(8)
对于电解液相,电荷守恒表达式如式(9)所示,其中σleff为电解液等效电导率,f±为平均摩尔活度系数,t+为电解液锂离子传递系数,cl为电解液锂离子浓度。多孔电极孔隙内部电解液等效电导率可用式(10)计算,其中σl为电解液的固有电导率,εl为电极孔隙率。对于多孔电极外电解质,εl = 1。
(9)
(10)
(3) 质量守恒方程
电极活性材料颗粒可近似为球形,根据Fick第二定律,活性粒子质量守恒方程如式(11)所示。其中r∈(0, Rs)为径向坐标,其中Rs为活性材料颗粒半径;cs(r, t)为活性颗粒的浓度。在球形颗粒表面及中心的守恒方程分别为式(12)及式(13)。其中活性颗粒固相扩散系数Ds与温度相关,如式(14)所示,Ds,ref为参考温度下的固相扩散系数,Ead为扩散活化能。
(11)
(12)
(13)
(14)
锂离子在电解液中的传递包括扩散和迁移,其中扩散过程可用浓溶液理论描述。其守恒方程如式(15)所示。其中Dleff为锂离子在电解液中的有效扩散系数,在多孔电极孔隙内部的有效扩散系数可由式(16)计算,Dl为锂离子在电解液中的固有扩散系数。
(15)
(16)
(4) 能量守恒方程
在电池三维分层最小电池单元结构计算过程,不考虑与环境的对流及辐射换热,因此能量守恒可用式(17)描述,其中ρ为材料密度,cp为材料比热容;等号右边第一项为可逆反应热,第二项为极化产热,第三项为欧姆产热。对于集流体及隔膜区域,仅有欧姆热。
(17)
1.2.2模型参数
式(5)中正、负电极材料参考电势Ueq,ref通过0.1 C放电倍率工况下的纽扣半电池测量,如图2所示,其中电池的荷电状态(SOC)定义为cs/cs,max。正、负电极的温度电阻系数(dU/dT)分别取自文献[14]及[15],如图3所示。式(18)及式(19)所示分别为式(9)中电解液电导率σl为及活度相关参数。式(20)为电解液相锂离子扩散系数。模型所需具体参数如表1所示。
图2 正、负极材料参考开路电势
图3 正、负极材料温度电阻系数
(18)
(19)
(20)
表1 模型参数
注: 上标Est为计算或估算值,上标Fit为辨识值,其余未标注的为测试值。
1.2.3模型计算及边界条件
本文研究不同极耳分布的电池分层结构最小单元在0.5 C、0.75 C、1 C、1.5 C及2 C等恒流放电倍率时的温度分布及电流密度分布均匀性,采用多物理仿真软件计算。如图1(b)所示,铜箔及铝箔外壁面边界设置为对称边界,正极耳顶面设置恒电流边界,负极耳顶面设置接地边界,其余边界均为绝热绝缘。
2 实验验证2.1实验方法为验证模型的可靠性,本文通过实验验证0.5 C、1 C、2 C放电倍率时模型的可靠性。实验方法如下。
电池预处理:以0.5 C(45 A)放电至截止电压2.5 V,搁置1 h,后以0.5 C恒流恒压充电至截止电压3.65 V及截止电流4.5 A,搁置一小时。
实验过程:如图4(a)所示,90 A·h样品电池通过与充放电柜正负极端子连接;热电偶贴于电池大侧面中心位置;随后用50 mm厚度的橡塑保温棉[k = 0.04 W/(m·K)]将电池六面包裹,以减少电池与环境的热交换。实验采用10 V/100 A充放电柜(新威BTS 10 V 300 A)对电池进行恒流放电,采用HOIKI LR8400数据采集仪监测电池温度。测试实物图如图4(b)所示。
图4 实验测试简图:(a)示意图;(b)实物图
2.2结果比较图5所示为恒流放电过程实验(Exp)与仿真(Sim)的电压对比曲线。如图所示,不同倍率放电过程的终止时间(即放电容量)接近,不同倍率放电过程的电压平台亦差别不大,说明模型可较好地预测电池端电压,同时认为模型计算得到的电池的电化学性能可靠。放电过程温度对比曲线如图6所示,不同倍率放电过程温度变化整体趋势基本一致。0.5 C放电终止时,实验和仿真温度相差0.57 ℃;1 C放电终止温差时为1.3 ℃;2 C终止温差为5.68 ℃。随着放电倍率的增大,绝对误差越大。其原因为仿真过程电池壁面边界条件为绝热,而实验过程电池向环境散热无法避免。电池温度越高(与环境温差越大),散热的热流密度越大。从整体上看,恒流放电过程实验和仿真的温度及电压曲线均吻合较好,因此认为模型可用于进一步分析电池的电化学特性及热特性。
图5 恒流放电过程中电池电压变化
图6 恒流放电过程电池表面温度变化
3 结果分析与讨论基于上述模型可靠性验证,下文分析皆采用仿真计算结果。
3.1温度及电流密度分布分析图7所示为2 C放电终止时刻最小电池单元的温度分布云图及电解质相垂直于隔膜方向的离子电流密度分布云图。如图7(a)所示,原设计电池在2 C放电时,最高温出现在电池上部负极极耳处,为61.55 ℃(电池初始温度为26.1 ℃);最低温出现在正极极耳处,为59.89 ℃;电池最大温差为1.66 ℃。如图7(b)所示,最大离子电流密度分布于电池中下部,为44.62 A/m2;最小离子电流密度分布于负极耳处,为42.62 A/m2;最大离子电流密度差值为2 A/m2。
图7 2 C放电终止时刻结果云图:(a)温度云图,℃;(b)离子电流密度云图,A/m2
图8所示为不同放电倍率终止时刻电池的最大温升(Tincrement)及自身最大温差值(Tdifference)。当放电倍率从0.5 C提高到2 C,电池最大温升以凸型曲线的变化趋势从12.43 ℃增大到33.88 ℃,电池自身最大温差以凹型曲线的变化趋势从0.1036 ℃增加到1.6645 ℃。意味着随着放电倍率的进一步提高,电池最大温差将进一步显著提高,而最大温升的增大速度相对放缓。
图8 放电终止时刻温升及电池温差随倍率的变化
图9所示为不同倍率放电终止时刻垂直于隔膜方向的平均离子电流密度(current density)及电流密度最大差值(current difference)的变化图。随着放电倍率的增长,平均电流密度从0.5 C时的11.01 A/m2线性提高到2 C时的43.62 A/m2,电流密度最大差值同样以线性增长的方式从0.5 C时的0.19 A/m2线性提高到2 C时的2 A/m2。
图9 放电终止时刻平均离子电流密度及电流密度最大差值随倍率的变化
由于原设计电池在放电过程顶部温度比底部高,当采用2 C倍率放电时,温差达到了1.66 ℃。而方形铝壳电池通常采用底部冷板散热的方式对电池进行降温,电池自身温差将进一步提高。另外大倍率放电时,垂直于隔膜方向的离子电流密度差值也较大。温度差及电流密度差值过大会致使电池局部老化过快,进而影响电池循环寿命及安全性。下文将分析极耳结构对温度分布及电流密度分布的影响,以期提高电池温度场及电流密度场的均匀性。
3.2极耳结构优化原设计放电过程上部负极区域温度高,为提高其温度均匀性,可增大负极耳的宽度,或减小正极耳的宽度。然而受安全阀位置及尺寸的影响,上部负极耳的尺寸难以进一步提高,因此本文采用减小正极耳的宽度的方法,来提高电池特性的均匀性。
由于极耳仅有电流通过的焦耳热,因此极耳电阻Rt极为关键,其计算如式(21)所示
(21)
为提高普适性,本文定义负极耳电阻Rtneg与正极耳电阻Rtpos的比值Sc,即式(22)所示
(22)
计算得到本研究电池对象的Rtneg = 1.832 mΩ,Rtneg = 0.5549 mΩ,即Sc = 3.30。另设置一系列的Sc,其对应的正极耳宽度如表2所示。
表2 正极耳宽度及电阻比
本部分分析电池的均匀性均采用2 C放电终止时刻的计算结果。图10所示为所选4组Sc对应的温度分布云图。当Sc从3.3降低到1.5时,电池正极耳处温度提高,但依然比正极耳高;当Sc降低至0.875时;正极耳处与负极耳处的温度接近;当Sc降低至0.625时,电池最高温从负极耳处转移到正极耳处。图11所示为不同Sc时的离子电流密度分布云图,从温度标签看,不同Sc时的最大及最小电流密度值均变化不大。另外最大值依然分布于电池中部,最小值分布于电池负极耳处。唯一不同的是,随着Sc的减少,正极耳附近的离子电流密度逐渐减小。
图10 不同Sc时放电终止时刻温度分布云图
图11 不同Sc时放电终止时刻离子电流密度分布云图
图12所示为不同Sc时2 C放电终止时刻电池最大温升及温差的变化曲线图。所示当Sc = 0.875时,电池温差最小,为1.1955 ℃。当Sc低于0.875时,温差随Sc的降低而增加显著,其平均斜率绝对值为5.2 ℃/Sc。当Sc高于0.875时,温差随Sc提高的变化斜率绝对值远小于Sc低于0.875时的值,其平均斜率为0.1934 ℃/Sc。Sc=0.875亦为温升变化的拐点。Sc小于0.875时,温升平均变化速率绝对值为1.52 ℃/Sc。大于0.875时,变化速率显著放缓,其绝对值为0.2021 ℃/Sc。说明温度均匀性最优的Sc值在0.875附近。
图12 不同Sc时放电终止时刻电池最大温升及温差
图13所示为不同Sc时2 C放电终止时刻垂直于隔膜方向的平均离子电流密度及电流密度差值曲线图。所示平均电流密度及差值在Sc小于1.5时有轻微波动,平均电流密度的波动幅度为0.1A/m2,而电流密度差的波动为0.02 A/m2。由于波动较小,因此可认为电流密度及其差值受Sc的影响不大。
图13 不同Sc时放电终止时刻最大离子电流密度及电流密度差值
4 结 论本文采用基于三维分层结构的电化学-热耦合模型,研究对侧极耳分布的方形铝壳电池的内部电芯的电场及温度场特征,并优化其极耳尺寸,所得结论如下。
(1)在0.5~2 C范围,随着放电倍率的增大,电池最大温升以凸型曲线的趋势升高,电池自身最大温差以凹型曲线的趋势增大,电解质相垂直于隔膜方向的平均电流密度及电流密度分布的最大差值呈线性增长。
(2)2 C放电时电池最大温升及温差与负极耳和正极耳的电阻比Sc显著相关,最优的Sc值被认为在0.875附近。当Sc小于0.875时,电池最大温差以5.2 ℃/Sc的速率快速降低,电池最大温升以1.52 ℃/Sc的速率快速下降;当Sc大于0.875时,电池最大温差以0.1934 ℃/Sc的速率缓慢上升,最大温升以0.2021 ℃/Sc的缓慢速率下降。
(3)垂直于隔膜方向的平均离子电流密度及电流密度差值受Sc值的影响较小。在Sc为0.5~3.3内,平均电流密度的波动幅度为0.1A/m2,而电流密度差的波动仅为0.02 A/m2。
本文基于三维分层结构模型来优化电池极耳尺寸,较基于集总参数法的三维模型更为准确。然而受计算量限制,本文仅针对电池的最小单元(共5层)进行计算。为获得更为精确的仿真结果,下一步将构建基于分层结构的全尺寸电池电化学-热耦合模型。
引用本文: 陈才星,牛慧昌,陆瑞强等.基于三维分层结构的锂离子电池电化学-热耦合仿真及极耳优化[J].储能科学与技术,2020,09(03):831-839.
CHEN Caixing,NIU Huichang,LU Ruiqiang,et al.Electrochemical-thermal coupled simulation and tab optimization of lithium ion battery based on three-dimensional multi-layer structure[J].Energy Storage Science and Technology,2020,09(03):831-839.
以上就是关于智慧pos机聚合物锂电池,基于三维分层结构的锂离子电池电化学的知识,后面我们会继续为大家整理关于智慧pos机聚合物锂电池的知识,希望能够帮助到大家!
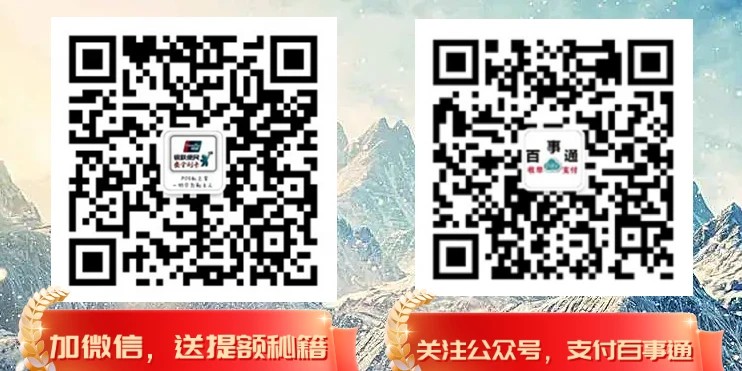